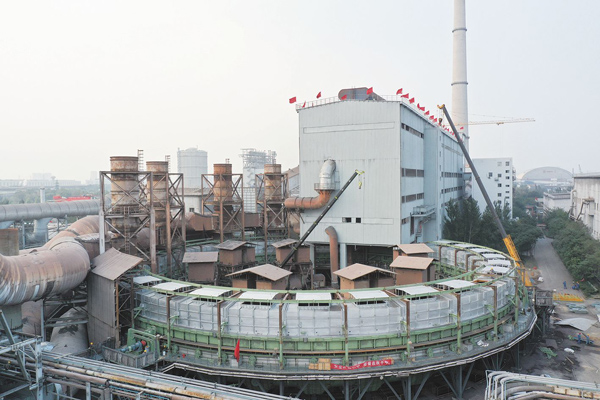
中冶北方承擔(dān)的山西太鋼四燒715m2多功能高效環(huán)冷機(jī)改造工程
本報通訊員 李迪
“綠色制造”作為一個現(xiàn)代化的制造模式,是推動冶金行業(yè)轉(zhuǎn)型升級的必由之路,是化解產(chǎn)能過剩、產(chǎn)業(yè)發(fā)展的戰(zhàn)略方向。在冶金行業(yè)鐵前領(lǐng)域,燒結(jié)廠毫無疑問是鋼鐵企業(yè)推行“綠色制造”戰(zhàn)略重點(diǎn),不僅因為其煙氣排放量占鋼鐵企業(yè)總排放量的一半以上,更因為燒結(jié)煙氣具有排放量大、溫度高、攜帶粉塵多、含二噁英類物質(zhì)等特點(diǎn),使其成為名副其實的“大氣殺手”。近年來,中冶北方積極開拓冶金鐵前領(lǐng)域節(jié)能環(huán)保市場,以超低排放改造項目為發(fā)力點(diǎn),研發(fā)應(yīng)用了一系列滿足鋼鐵企業(yè)環(huán)保改造的核心技術(shù),提供一站式節(jié)能環(huán)保定制服務(wù),助力鋼鐵企業(yè)打贏“藍(lán)天保衛(wèi)戰(zhàn)”。
確立全過程煙氣治理的技術(shù)路線
提到煙氣治理,人們第一個想到的就是脫硫脫硝裝置,其可以綜合脫除煙氣中的有害物質(zhì),使得外排的煙氣符合國家環(huán)保排放標(biāo)準(zhǔn)。但是,脫硫脫硝裝置的建設(shè)投資和生產(chǎn)成本會隨著煙氣處理量的增加而大幅提高,對于鋼鐵企業(yè)來說是不能承受之痛。因此,針對燒結(jié)廠進(jìn)行超低排放改造,僅僅關(guān)注末端治理(除塵、脫硫、脫硝)是遠(yuǎn)遠(yuǎn)不夠的。要把目光轉(zhuǎn)向燒結(jié)生產(chǎn)全過程,要關(guān)注原料條件、燃料條件、設(shè)備狀況、生產(chǎn)操作、檢修維護(hù)等因素的影響,具體措施要從源頭、過程、末端全方位切入,綜合考慮煙氣治理的建設(shè)投資和節(jié)能減排效果。對此,中冶北方確立了采用“源頭控制”“過程優(yōu)化”“末端治理”“余熱利用”相結(jié)合的技術(shù)路線進(jìn)行燒結(jié)煙氣的綜合治理,用最高的性價比幫助鋼鐵企業(yè)完成環(huán)保改造。
循著這樣的技術(shù)路線,中冶北方著眼燒結(jié)生產(chǎn)全過程和關(guān)鍵環(huán)節(jié),分兵突圍、各個擊破,潛心10余年進(jìn)行技術(shù)研發(fā)和創(chuàng)新,最終形成了煙氣循環(huán)工藝、活性焦煙氣凈化技術(shù)以及燒結(jié)余熱資源高效回收與利用技術(shù)“三把利刃”——“煙氣循環(huán)工藝”將一部分煙氣循環(huán)利用,可實現(xiàn)“源頭控制”和“過程優(yōu)化”,大幅降低了后續(xù)凈化風(fēng)量,節(jié)省了脫硫脫硝裝置的投資和運(yùn)行費(fèi)用;“活性焦煙氣凈化技術(shù)”具有完全自主知識產(chǎn)權(quán),設(shè)備全部國產(chǎn)化,可實現(xiàn)煙氣中污染物五位一體脫除,達(dá)到超低排放要求;“燒結(jié)余熱資源高效回收與利用技術(shù)”集成了多功能高效燒結(jié)環(huán)冷機(jī)成套技術(shù)及燒結(jié)余熱高效利用技術(shù),通過合理配置環(huán)冷機(jī)的冷卻風(fēng)、降低燒結(jié)和冷卻系統(tǒng)漏風(fēng)率等措施,實現(xiàn)燒結(jié)礦顯熱和燒結(jié)煙氣顯熱的高效回收,然后將回收得到的余熱進(jìn)行梯級利用。
定制服務(wù)提供高效環(huán)保解決方案
市場是檢驗技術(shù)創(chuàng)新的“試金石”,每一項新技術(shù)、新工藝的最終歸宿都是服務(wù)于市場和客戶。針對不同鋼鐵企業(yè)新建、改造、擴(kuò)產(chǎn)的需求,中冶北方充分利用這3種技術(shù)的不同作用和優(yōu)勢,因地制宜,各取所長,為客戶提供高效的定制化環(huán)保解決方案。
2013年,中冶北方設(shè)計的國內(nèi)第一套燒結(jié)煙氣循環(huán)系統(tǒng)在寧鋼新技術(shù)燒結(jié)機(jī)上順利投運(yùn),系統(tǒng)投運(yùn)近一年的運(yùn)行結(jié)果表明,煙氣循環(huán)利用對燒結(jié)礦產(chǎn)質(zhì)量無明顯影響,工序能耗降低約5%,外排煙氣可減少20%以上,煙氣脫硫裝置投資及運(yùn)行成本可減少約20%。節(jié)能、減排、降本的燒結(jié)煙氣循環(huán)技術(shù)在寧鋼成功應(yīng)用,填補(bǔ)了國內(nèi)該領(lǐng)域的技術(shù)空白,成為國內(nèi)自主研發(fā)的燒結(jié)煙氣循環(huán)技術(shù)應(yīng)用的里程碑。
2015年4月,中冶北方總承包建設(shè)的國內(nèi)第一套具有完全自主知識產(chǎn)權(quán)、設(shè)備全部國產(chǎn)化的燒結(jié)煙氣活性焦凈化裝置——永鋼聯(lián)峰鋼鐵450m2活性焦煙氣凈化工程建成投運(yùn)。該項目綜合運(yùn)用了煙氣循環(huán)技術(shù)、活性焦煙氣凈化技術(shù)以及多功能高效環(huán)冷機(jī)技術(shù),采用先減量后治理的思路,減排、協(xié)同治理與余熱利用并舉,使活性焦煙氣凈化系統(tǒng)的處理風(fēng)量降低了30%,投資節(jié)省30%,噸礦煙氣凈化運(yùn)行費(fèi)用降低20%,新燒結(jié)機(jī)系統(tǒng)建成后減排效果顯著,每年可減少二氧化硫排放9210噸、粉塵排放670噸、氮氧化物排放1758噸和生產(chǎn)濃硫酸約1.5萬噸,每年減少向大氣中排放約33.6億標(biāo)準(zhǔn)立方米燒結(jié)煙氣,為鋼鐵行業(yè)節(jié)能減排提供了新的思路。
持續(xù)改進(jìn)
確保技術(shù)水平行業(yè)領(lǐng)先
2018年初,國家再推環(huán)保新政策,燒結(jié)、球團(tuán)煙氣超低排放標(biāo)準(zhǔn)應(yīng)時而出。中冶北方無畏挑戰(zhàn),先后承攬了濟(jì)源鋼鐵、聯(lián)峰鋼鐵、日照鋼鐵、天柱鋼鐵等10余個燒結(jié)超低排放改造和新建項目,并在項目實踐中持續(xù)改進(jìn)和優(yōu)化提升技術(shù)裝備水平:煙氣循環(huán)技術(shù)的應(yīng)用場景更加廣泛,可以結(jié)合各家企業(yè)自身的實際條件和需求,站在不同的角度,有針對性地實施合理的工藝方案;活性焦煙氣凈化技術(shù)的脫硫脫硝效率從原來的95%以上提高到98%以上,并在凈化系統(tǒng)增設(shè)煙道氣-氣換熱器,利用燒結(jié)煙氣的余熱產(chǎn)生熱水,循環(huán)利用,在有效控制進(jìn)入吸附塔的煙氣溫度的同時,確?;钚越瓜到y(tǒng)穩(wěn)定運(yùn)行;多功能高效環(huán)冷機(jī)技術(shù)從第一代產(chǎn)品更迭到第六代產(chǎn)品,產(chǎn)品遍布遼寧、江蘇、山西、山東等國內(nèi)多個省以及越南等“一帶一路”沿線國家,真正做到了以持續(xù)不斷的創(chuàng)新引領(lǐng)行業(yè)技術(shù)進(jìn)步,為冶金行業(yè)實現(xiàn)綠色發(fā)展提供新的思路和解決方案。
在開啟全面建設(shè)社會主義現(xiàn)代化國家新征程中,中冶北方將繼續(xù)聚焦綠色制造,加大節(jié)能減排技術(shù)的研發(fā)和推廣力度,圍繞提高活性焦綜合性能、提高污染物脫除率、降低裝置運(yùn)行費(fèi)用及環(huán)冷機(jī)零排放技術(shù)進(jìn)行深度研發(fā),加快形成大氣污染物多種治理方案技術(shù)集成以及工業(yè)廢水綜合治理工藝技術(shù)集成。中冶北方將深化自主研發(fā)和產(chǎn)學(xué)研合作的協(xié)同創(chuàng)新機(jī)制,在提升創(chuàng)新研發(fā)的自主可控能力的前提下,加強(qiáng)與高校、鋼企的合作與交流,加速“拳頭產(chǎn)品”的轉(zhuǎn)化落地,進(jìn)一步發(fā)揮科技創(chuàng)新的支撐引領(lǐng)作用,夯實“國家隊”核心技術(shù)儲備。
《中國冶金報》(2021年7月13日 05版五版)